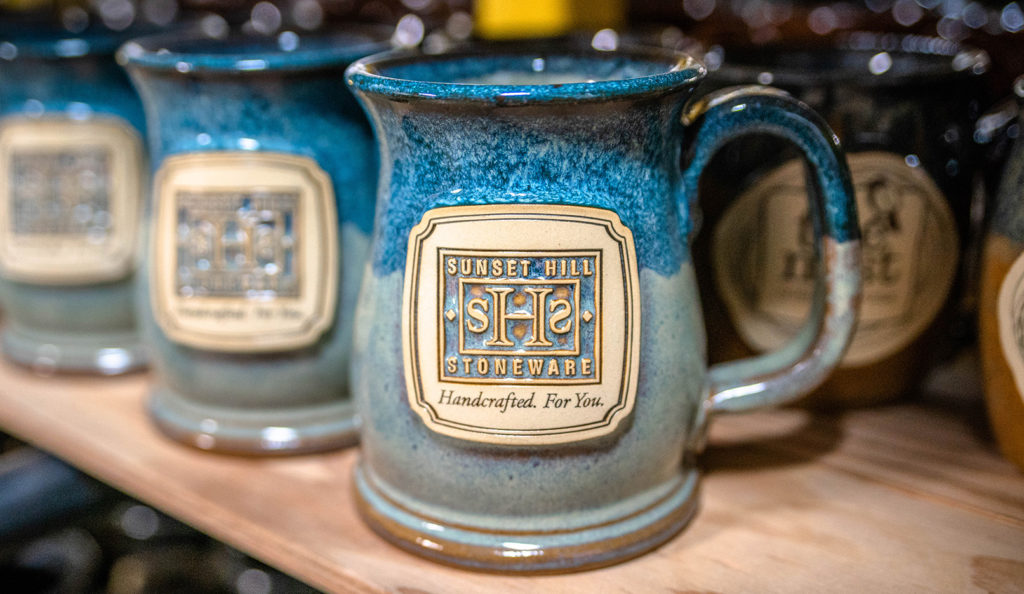
Sunset Hill Stoneware
Sunset Hill Stoneware is an American-based company that specializes in wholesale coffee mugs. Our team of artisans handcrafts all of our products in Neenah, Wis. and specializes in setting your logo or artwork in stone. While we primarily make stoneware coffee mugs and beer mugs, our catalog offers other USA-made products as well, all of which add elegance and quality to your brand.
If you’re looking for a deep dive into whether working with our company is right for you, you’ve come to the right place.
Table of Contents
- About Sunset Hill Stoneware
- History of Sunset Hill Stoneware
- Custom Technology at Sunset Hill Stoneware
- The Artisans at Sunset Hill Stoneware
- Our World Record-Breaker
- Who We Are and What We Care About
1. About Sunset Hill Stoneware
Sunset Hill Stoneware prides itself on its USA-made stoneware. Although we’ve experimented with other types of promotional products before, stoneware has always been our bread and butter. We’ve also mastered our craft to the point that we’re proud to say we offer some of the most elegant mugs you’ll ever use. You can also expect to get your mugs faster than anywhere else in America.
On top of that, we strive to take care of the environment, both inside and outside our shop. Our business is paperless, using an electronic MRP and other systems to greatly reduce the amount of paper we throw away every year. Since firing our mugs takes a lot of electricity, we also recycle the heat they put out and use it to power our shop.
We also care deeply about the members of our team. They’ve shown us time and again that they care about getting the job done right. In turn, we use innovation to keep them safe at work. However, just like most businesses, we had humble beginnings.
2. History of Sunset Hill Stoneware
Sunset Hill Stoneware began life in an old firehouse in the village of Dale, Wis. in 1998. Owner and CEO Tom Dunsirn started the company after college with his love for hand thrown pottery. Originally named Fox Valley Stoneware, Tom and a friend turned clay into mugs in a deserted firehouse in Dale, a small township outside the Fox Valley. The first lease was handwritten in pencil on the back of a place mat and that pottery studio became the company’s location for the next 14 years. Thus began the early days of Sunset Hill Stoneware.
Since the earliest chapters in the history of Sunset Hill Stoneware, Tom’s father, Duane has contributed to helping our business grow. Although he wasn’t sure this was the right career path for Tom, Duane came to the pottery studio from time to time and engineered new tools and processes to support our business. After seeing how Tom grew the business, Duane joined the company as a co-owner and was a frequent visitor at our shop while he developed custom technology.
For a time, Sunset Hill Stoneware had a retail store located in Dale. We also had a storefront in Neenah and worked with local businesses like the Hang Up Gallery to bring our mugs to the world. However, as we grew, we realized that our true calling was in wholesale pottery mugs. We also focused on what we do best, with coffee mugs and beer steins becoming our focus. Before that, we’d also made everything from vases to wine goblets on a regular basis.
Then, in 2012, we outgrew the space we used. After spending the first 14 years of its life in Dale, SHS moved to Neenah and upgraded itself with a brand-new production facility that we could better outfit with our technology. Eventually, we came out with new branding to match. Out went the earthy brown logo, in came our current, sleeker look in black and white.
In 2015, the two owners turned the industry upside down by putting the health and safety of their employees first. While continuously trying to protect their employees from circulating clay dust within the facility, it was a difficult task to control without major investment in clean-air systems. Their investment paid off when an independent environmental firm confirmed that their efforts and circulation systems maintained the continuous flow of fresh air desired—and beat stringent OSHA requirements.
We celebrated our 20th anniversary in 2018. Ever since then, we’ve been coming up with new products, offering individual mugs available on our SHS Collection and developing new glaze colors.
3. Custom Technology at Sunset Hill Stoneware
Duane has always had a mind for invention and innovation. Even when he ran his own businesses, he invented technology that’s now ubiquitous in everything from printed stickers to McDonald’s Monopoly game pieces. When Tom’s business at Sunset Hill Stoneware began to take off, Duane developed innovations you won’t find anywhere else. Here are a few pieces of custom technology we use that help make our employees safer and improve the quality of our stoneware mugs.
Pottery Wheels
The wheels our potters use are the NASCAR racers of the pottery world. With just the push of a pedal, they can operate faster than any standard pottery wheel. Duane also designed them to be lower maintenance than most pottery equipment, so our team can spend more time throwing mugs the way God intended and less time waiting for repairs.
By nature, pottery is an ergonomics nightmare. But, Duane’s designs minimize the work our potters have to do with their feet to keep the wheel turning. Because of this unusual design, each of our potters can make hundreds of stoneware mugs every day. We have eight of these pottery wheels in our facility—seven that our potters use every day and one that our master potter, Jason Sonsthagen, uses when he’s not managing the entire shop.
Ventilation
In most pottery studios, the air quality is bad enough that the potters have to wear personal ventilators to keep the clay dust out of their lungs. Failure to do so could cause diseases like silicosis or lung cancer later on.
To prevent our employees from getting hurt, we use a custom ventilation system by Duane’s own design. It traps the dust that comes from our pottery before it can get into the air and puts it into a special filtration system.
Working in tandem with this, we have a custom HVAC system that keeps our shop at the optimal temperature and humidity levels so our stoneware dries at the same rate every time we make it. No matter if it’s -10° F outside in February or the most humid day in summer, our stoneware mugs will dry at the same rate every time.
Safety Features
As mentioned previously, we care about keeping our employees safe. One of the key ways we do that is with custom filtration systems.
Pottery is an infamously dirty industry. It’s not uncommon for potters to develop diseases like silicosis later in life. This happens because when pottery clay dries, it turns into fine particles. These particles are so small that they get trapped in the lungs and build up over time, causing major health problems later on.
Our filtration systems trap the particles of clay before they can become airborne, keeping our crew safe. Our team also doesn’t have to wear ventilators or dust masks while they work like so many potters do. We’ve even had representatives from OSHA come in and test the air in our shop to make sure.
We’ve also got some tricks to avoid chronic injury and pain at work. Our potters store their slugs of clay on elevated platforms so they don’t have to bend as far.
4. The Artisans at Sunset Hill Stoneware
Each employee at Sunset Hill Stoneware is an artisan and an expert on stoneware in their own right. Every part of the process requires nuance and a keen eye for details. Here is a glimpse at some of the jobs we have working at our company. You can also meet each member of our team in our ongoing series that puts a new person in the spotlight each month.
Potters
Each potter on our team is skilled and underwent extensive training before they started throwing full time. It’s an art that requires a gentle hand and a keen sense of touch, along with strength in the arms.
All of our potters have a slightly different method of making their handcrafted mugs. How they do it depends on what they found was most comfortable for them when they learned to throw, and which hand is dominant for them, among other things. They’re so distinct from each other that Jason can tell who made a piece by looking at its ridges and swirls.
Handlers
Our handlers have to use a very delicate touch when they apply the handles and medallions to your custom handmade mugs. Failure to do so could make the mug collapse.
Few handles will look exactly alike on your mugs. Part of this is because our handling team applies the handles with their thumbs, leaving behind a unique print each time. Each person also has a slightly different way of attaching your handle to the mug.
After they’ve applied the handles, this team also applies the medallions to your mugs. Once they’ve done that, the mugs are ready to air dry and move to the next station in our shop.
Preppers
Our prepping, waxing and stamping crew covers a few different steps. They sand the bottoms of each mug to make it smooth enough that it won’t scratch your counters. They also apply a custom stamp in potter’s wax, so you know when you’ve found a Sunset Hill Stoneware mug. This stamp might also have different designs on it, depending on where you purchase it.
Ultimately, much of what our prepping team does involves fine details. The touches they add take your stoneware coffee mug from being a typical mug to the best coffee mug around.
Glazers
Our crew of glazers applies the mineral-based glazes that add color and durability to your mugs and steins. However, glazing requires more finesse than you might initially believe. It’s a discipline that requires you to get the timing and position exactly right. Very few people can do it correctly on the first try.
Working with our prepping team, the glazing team also develops new glazes and loads your mugs into the kilns for each firing stage. You can learn more about why we fire our mugs more than once on our blog.
Shippers
Our shipping team does more than pack up your mugs and send them out. They’re also experts in quality control.
During our busiest season, each person on the shipping team inspects thousands of mugs daily. They also catch any minor mistakes or blemishes on our mugs, fixing them if possible, so we can send you the best product we’re capable of making.
Graphic Design
Our graphic design department adapts your logo or artwork onto our medallion. This team produces hundreds of artworks each week for our shop, all year long. They’re skilled artists that can capture photographic detail, down to the siding on Victorian houses.
However, their artistic endeavors don’t end after they clock out. They also specialize in crafting, hand-lettering and other design work, as well as beekeeping.
Sales and Customer Care
Our sales squad is a team of experts that know which color and mug style will pair with your logo. They’re always paying attention to how each glaze behaves, and the nuances that will help your logo look its very best on our mugs. They’re also trained to help out in the rare event that something does go wrong, which is where their customer care expertise comes into play. At the end of the day, they want you to be happy with your stoneware. They’ll also go the extra mile to make that happen.
Even more, many of our team members have their own art projects that they do once they’re finish making mugs. You can learn more about each of them in our ongoing series, and by following us on social media.
Marketing
Without our marketing crew, you probably wouldn’t know who we are—or what Sunset Hill Stoneware is. Our marketing team does everything from runs advertisements on Google and YouTube to interacting with local TV stations to posting on our Facebook and Instagram pages. They also let the world know about the single mugs we make for our Amazon page, and connect with customers so you know where to find your mugs. You also wouldn’t be reading this without them.
Although you might not always interact with our marketing team directly, you might find them outside work in everything from robotics competitions to Irish dance shows. Keep your eyes peeled.
5. Our World Record-Breaker
In our 21st year, a member of our team became the fastest potter in the world.
Michael Weber knew he wanted to go for a Guinness World Record long before the day of his attempt. So, he trained for at least 30 minutes a day in the months leading up to it. Like one would train for a marathon, Mike began by building up his endurance. Along the way though, he needed to make some changes from how our plant manager, Jason, trained him.
Since he doesn’t create the pots he threw for his world record as part of our catalog, he had to adjust his method so that he could throw the clay, pull it into the proper shape and cut it off the wheel with a wire within a matter of seconds.
Although he was already one of our fastest potters, shaving seconds off his attempt was a core part of his training. One of the biggest differences he made was shaping each slug into a sphere so it was easier to manipulate. He also marked his water bucket so he could easily tell if he was within the required dimensions.
Mike also had a small team acting as his pit crew during his attempt. These three fellow potters fed him round slugs of clay, set down boards for him to use for his completed pots and taking them away once he filled them. Without having to worry about these factors, Mike could focus on just throwing.
In the days leading up to the attempt, he could throw one pot in 15 seconds. However, the moment of truth would come on Nov. 14, 2019.
Mike and his crew came to the shop around 5 a.m. that morning. This not only gave him the chance to prepare himself, but also to talk to reporters and coordinate with his pit crew.
By his own admission, Mike was nervous in the hours and minutes leading up to his attempt. But, he was also excited. Needless to say, he didn’t sleep much the night before the big day.
Once the clock struck 7 a.m., Mike was off. After overcoming his nerves with the first few pots, Mike found a steady pace. Only a handful of his pots weren’t up to our experts’ standards. By his own admission, Mike told us afterward that he slowed down during the middle of the attempt. However, he managed to rally near the end with the support of his pit crew and coworkers watching him work.
By the time the hour was up, Mike threw 212 pots. This shattered the existing record of 193, making Mike the new world record holder.
You can view Mike’s world record run in its entirety on Facebook and YouTube.
6. Who We Are and What We Care About
It goes without saying that we’re persnickety about what we do. But, that’s only because we care, aggressively. We care about taking care of the earth, producing a quality product and helping our neighbors. Here are just a few of the causes we support and events that changed us.
Veterans and Military
Our company president is a Marine Corps veteran, and we have other teammates who have served in the Air Force and National Guard. We also support dozens of veteran-run groups and businesses with our mugs. While some of these are traditional businesses, others also support their fellow veterans through mental health.
Some of our customers also include active military units looking for gifts for their members. Whether it’s for the prestigious Marine Corps Security Guard Detachments at embassies in China or at Camp Dahlke in Afghanistan, we’re happy to send mugs to these troops deployed overseas.
Environmental Groups
We make our product with minerals that come from the earth and water that comes from our lakes and rivers. Because of this, we want to support our natural resources and work with other groups who do. We also work with groups that focus on wildlife conservation.
Some of the groups Sunset Hill Stoneware supports are aquariums that focus on reducing water pollution, conservation and improving sustainability for seafood stocks worldwide. Other groups protect America’s wilderness areas from industrial development. We’re proud to support these groups through their mug sales and other fundraising efforts.
The Art Community
Sunset Hill Stoneware is a company full of artists. We’re always looking for ways to connect with our local arts community, by connecting with local art shows and helping high school students in our area discover pottery as a medium. We’ve sponsored local art shows like Neenah Uncovered, Warm Her Heart and Bazaar After Dark with Future Neenah in the past, supported our friends at High Cliff Studio and had our own team members in even more shows.
Having Fun
We take our work seriously, but our team also has a lot of fun. We’ve gone on missions to catch leprechauns, found some of the haunted secrets at our office and had an encounter with Krampus during the holiday season. We also dabbled in the art of coffee on April Fool’s Day. This is something we try to focus on all year long though, so stay tuned with us to see what we’re up to next.
[…] team from being able to work at first. For most of April, you could only find three people in Sunset Hill Stoneware’s shop: Chris Rand, our company president; Jason Sonsthagen, our production manager; and Jon Burke, […]
[…] a colorful history leading up to when it became what it is today. With Memorial Day just days away, Sunset Hill Stoneware takes a closer look at the strange history behind Arlington National […]
[…] any point throughout the year, Sunset Hill Stoneware’s delivery time for your custom mugs can vary by a range of several weeks, especially during our […]