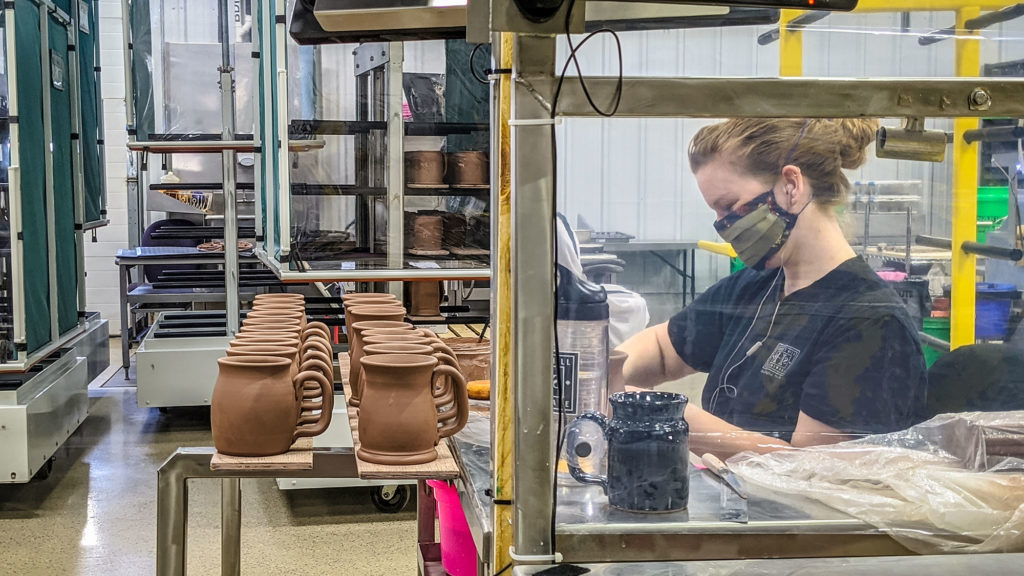
How American Manufacturing is Getting Back to Work
As a country, the current COVID-19 crisis has set us back. Thousands of Americans have died. Millions have gotten sick. Even more have been forced out of work. However, we’re starting to get back on our feet. It’s not a process that can happen immediately, but we’re taking every step we can to get the American worker back to their job. This is a glimpse at how American manufacturing is getting back to work in the wake of a pandemic.
Keeping the Shop Running During Shutdown
In our home state of Wisconsin, we had a strict Safer at Home order that prevented our production team from being able to work at first. For most of April, you could only find three people in Sunset Hill Stoneware’s shop: Chris Rand, our company president; Jason Sonsthagen, our production manager; and Jon Burke, our maintenance manager. These three kept our shop in working condition while the rest of us were away.
This dire situation also presented us with some opportunities we wouldn’t normally have. We were able to do some cleaning and maintenance that we couldn’t normally do with our whole crew at work. That includes making sure our kilns are healthy and that all the technology we use is in working condition.
However, there were some time-sensitive orders for us to fill. Since some customers needed their orders in time for Memorial Day, Jason threw all of the mugs himself. Chris also got some hands-on experience making mugs, learning how to apply handles and medallions. Together, the two produced about 50 mugs each day.
When he wasn’t filling orders, Jason also used this downtime to develop new products. For those who may want fine art pieces from Sunset Hill Stoneware, he’s been making new, one-of-a-kind pieces like vases, pitchers and platters. You might find these unique works of fine art on our social media pages in the near future, so stay tuned.
On top of that, he mastered the recipe for a few new glaze options. Coming soon, you might find a few new, long-requested colors and finishes, including the return of our yellow glazes. We’ve also got a line of matte options coming because Jason was able to focus solely on testing glazes during this downtime. Now, he’s just putting the finishing touches on the recipe.
Resuming Operations after COVID-19
Given that many states still have rules in place to prevent COVID-19 from sickening more people, it’s impossible for most manufacturers to resume business as usual right away. Such is the case at Sunset Hill Stoneware. Our governor extended our Safer at Home order until the end of May. But, with the extension, his order allowed non-essential businesses to begin Minimum Basic Operations.
For us, that meant bringing back a small handful of our production crew to start producing our stoneware mugs again. We started with a small crew to get the process started, since it would be hard for us to go from producing 50 mugs with two people to several hundred overnight. During the first full week of May, however, we brought a slightly larger crew back to meet that quota.
How Sunset Hill Stoneware was Already Prepared
We’ve talked before about how we use custom technology to protect our employees and visitors. That same technology is now helping us protect them from COVID-19.
When we built our current facility eight years ago, co-owner Duane Dunsirn designed it with the idea of keeping our potters safe. Since most of our competing potteries are famous for having clay dust, oscillating fans and poor filtration systems, he wanted to make sure that nobody in our company would get sick due to the work they did. Part of that involved developing our Building Automation System (BAS) to filter out even the smallest particles and keep the climate controlled in our shop to prevent airborne dust.
To protect the artisans making your mugs, our air handling systems have multiple stages of filtration, according to maintenance manager Jon Burke. The last stage in each of these systems includes a MERV-13 in most areas and a MERV-15 filter on the production floor, plus HEPA filters on equipment where our crew is sanding mugs. Similar to the filtration systems used in hospital operating rooms, these filters are designed to trap particles that are a fraction of a micron in size.
“These are things we’ve had in place in this building for a while, not because of the coronavirus,” Jon explained. “We try to be diligent in scrubbing the air clean before it’s released back into the plant.”
Thanks to these filters, we were already prepared to meet the CDC’s guidelines for preventing COVID-19 from spreading in our shop. Jon also changed the filters immediately after we shut down production. Duane noted that we also flush the air out of the building before and after the working day to remove germs from the air daily.
Typically, we change the air filters once a month. However, with COVID-19, we’ve been looking into changing them even more frequently to keep our crew safe.
“I did this not for COVID-19, but because it was the right thing to do,” Duane said. “It was the right thing to do 10 years ago, and it’s the right thing to do now.”
CDC Guidance for Manufacturers
The CDC has issued multiple recommendations for manufacturers who are essential or returning to work.
Mike Starke, a nursing instructor at the RN to BSN program at SUNY Brockport, stressed that it’s crucial to follow these federal, state and local guidelines as manufacturers try to resume production. As we go forward in this crisis, he said some may even choose to split into shifts to reduce the amount of people in the building at the same time, to maintain social distancing.
Such is the case with other manufacturers who shut down during this crisis. Some, like our next door neighbors at Essity, have been working to keep up with demand for essentials like paper towels and bathroom tissue while following state guidelines. Many others, however, are learning to work with a reduced workforce in their plants, along with supply chain issues stemming from not being able to get raw materials from other parts of the world.
Sunset Hill Stoneware is lucky by contrast—we have all the materials we need for production. We’re also exploring different avenues for making sure our entire crew can safely get back to work. Just like everyone else, we are having trouble finding supplies like disinfecting wipes. However, we’ve made sure that the supplies we do have meet the CDC’s guidelines for sanitizing our building. Jon and Jason check the CDC and Wisconsin Department of Health Services websites for updates on a regular basis. All of this is to ensure we’re still ahead of the curve to protect our family.
“We’re watching every day because things change,” Jon said. “This is a very fluid, volatile situation, and we’re just trying to stay on top of it.”
A lot of Americans are also uneasy about going back to work. While we all still need to feed our families, many of us are afraid of getting severely ill in the process. That’s why Sunset Hill Stoneware is going to such lengths to ensure everyone’s safety.
“We’re trying to be as responsible as possible using the knowledge we have,” Chris explained. “We’re doing our best to preserve everyone’s safety, and their livelihood.”
Safety Precautions for Coronavirus in Manufacturing
Normally, we’re proud to say that as many as 20 different pairs of hands help make your mugs before they arrive at your door. But, that handmade process makes it harder to keep our employees safe as American manufacturing is getting back to work. That’s why we’ve added a few extra safety measures at the shop. Some of these are more visible than others.
Masks
Those who follow some of our team members on social media know that we’ve been preparing for weeks. One of our mothers has been sewing face masks so our crew has some extra protection. A few even have Superman and Batman patterns on them, so our potters called dibs as soon as they saw them.
We require everyone at the shop to wear one of these masks. We also have a supply of disposable masks available if we have visitors scheduled to come in.
Chris is encouraging those with masks to use them outside the shop, too. Following CDC guidelines, we’re requiring everyone to clean their masks between uses. All these steps are a larger part of reducing risks while we get back to doing what we do best.
“It’s going to be inconvenient to wear a mask, but it’s not just about you getting COVID-19,” Chris explained. “Maybe you’re lucky and you’re asymptomatic, but we’re a family. We need to take care of the rest of our family.”
Temperature Checks
Every morning, before work starts, we take our employees’ temperatures to make sure they’re normal. If they have a fever, we send them home. This falls in line with state requirements to make sure we aren’t making anyone work while they’re sick and potentially contagious.
With that, we also have a sign-in sheet that our administrative team uses to document anyone that comes in or out of the shop.
Plastic Barriers
There are some parts of our process that require our crew to be fewer than six feet apart from each other. For example, our medallion pressers usually stand close together when they’re making your medallions. To keep them safe, we’ve installed clear plastic barriers at some stations. These let our crew members work closely together and see each other while preventing the spread of COVID-19.
Gloves were already part of the process for some of our employees. However, we’ve been making sure that they’re widely available in the shop for anyone who might want to use them, just as we have with surgical masks.
Deep Cleaning
Safety and cleanliness are intertwined right now.
Our pottery facility was clean even before this pandemic started. However, we’re taking extra steps to protect our employees in high-traffic areas. Between clocking in and out for the day, and between breaks, we’ve been sanitizing all of the doorknobs, handles and other common surfaces. We also clean all of the keys on the punch clock, since everyone uses it multiple times a day.
Sunset Hill Stoneware is also using its custom technology to better protect its employees. We’ve talked before about the custom HVAC system that helps us produce custom coffee mugs faster than anywhere else. The system quietly cycles out air multiple times each day and keeps the humidity at a comfortable level for both our production process and our employees’ health—typically between 40–60% relative humidity. The controls also allow us to change these climate settings remotely as needed. It’s easily one of the most robust systems of its kind, according to Chris. Thanks to that system, we can operate essentially as we would on a normal day before the pandemic.
“Nobody else does what we do on a daily basis,” Jason said. “We’re constantly bringing fresh air in.”
Our owner, Tom Dunsirn, has taken the matter of deep cleaning into his own hands. He cleaned every dark nook and cranny in the shop while we were away. Since we’ve resumed production, he’s also been cleaning the bathrooms and using our floor cleaner after everyone goes home. He’s also turned the hose on practically every surface in the building. Fact aside that running the Zamboni-like floor cleaner is kind of fun, it also keeps our shop spotless for our crew.
However, Tom isn’t the only one putting in extra effort. We have a safety committee that’s helping keep the whole team safe during this pandemic. Even individual employees have stepped up to sanitize. For example, Rachel Hanzek, a member of our handling team, cleans the door handles, punch clock, garage door buttons and other surfaces multiple times a day. Between these extra steps and the time everyone takes to do their part, we’re confident that we can keep everyone healthy in our shop.
“It’s kind of nice to be in a company where cleanliness is a thing to begin with,” Jon said. “We already were in a good place when coronavirus hit us. We haven’t had to take really radical steps.”
Hand-Washing
This is a good opportunity for working Americans to implement basic health practices again, according to Starke. We can’t help but agree.
“Staying home when you’re not feeling well is something that gets overlooked a lot,” Starke explained. He also recommended that workers wash their hands frequently, with the right technique and for a proper amount of time. Not doing these things could get you and your coworkers sick and cause other setbacks.
Starke also recommended that businesses may want to take up to 15 minutes out of the day to go over the basics of social distancing. After all, it’s relatively easy for germs to spread in manufacturing settings. Going over the best practices may help prevent infection from spreading between coworkers further down the line.
This COVID-19 crisis won’t end until we have a vaccine. Even then, it could potentially take months until that vaccine is available to the masses. For now, our current situation is the new normal, so Sunset Hill Stoneware is doing everything it can to stay prepared.
We’re back to work. We’re here and ready to help our little slice of America get back on its feet. Although we can’t predict what this pandemic will bring us next, Sunset Hill Stoneware is ready to stand tall and support both America and our family by bringing them back to work while doing everything we can to keep them safe.