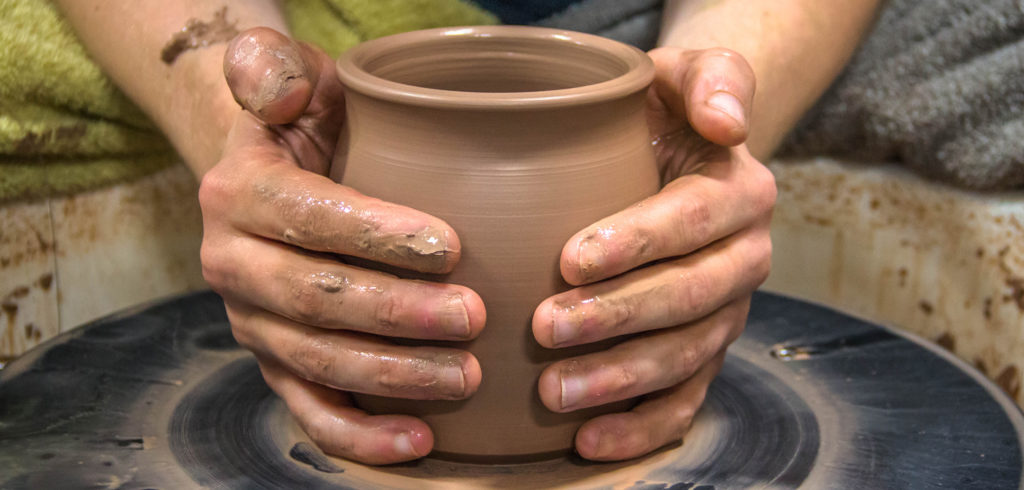
What is Stoneware?
Stoneware is dense pottery fired at high temperatures to make it resistant to liquids, or non-porous. It is made from clay, but is more durable than other kinds of pottery and earthenware.
Stoneware gets its name from its stone-like qualities. You can find it today in common household items like beer steins, crocks and coffee mugs. What sets stoneware apart from other pottery like porcelain or earthenware though? There are several factors that define stoneware and set it apart from other types of pottery.
Table of Contents
- What is the Difference between Ceramics and Pottery?
- Differences between Earthenware, Stoneware and Porcelain
- How is Stoneware Made?
- How to Handcraft Stoneware
- What are Ceramic Glazes
- History of Stoneware
- How is Stoneware Used Today?
- Get a Quote for Your Stoneware
What is the Difference between Ceramics and Pottery?
Pottery only uses clay. However, ceramics can have clay and other minerals that fortify it. These fortifications come in the form of glazes, mineral additives and other ingredients in the clay body that will make it more durable. Ceramics can also use minerals that aren’t clay, like zirconium oxide or plaster.
Because pottery consists of only clay, it is porous and not watertight. It’s also more fragile than ceramics, because there are no other minerals or glazes to fortify the mug. On the other hand, its fragility makes it perfect for etching intricate designs.
Cultures from all over the worlds have prized pottery for this reason for centuries, from ancient Greece to the Ashanti Empire and medieval Japan.
Today, most potters start out with more basic pottery before mastering ceramics. This allows them to develop their own methods and styles of working the clay on the pottery wheel before incorporating other minerals or additives.
Differences between Earthenware, Stoneware and Porcelain
Even though all three types of pottery begin with clay, the processes potters use to make them can differ widely. Here are a few of those key differences in a nutshell.
Earthenware
Potters have fired earthenware in ovens for thousands of years. During the height of the Roman Empire, it was used as amphorae to transport wine and olive oil to the farthest corners of their territory. But, liquids could penetrate these vessels, so goods like oil would often go rancid with repeat or prolonged use.
Unlike stoneware and porcelain, it only needs firing temperatures of 1,200° F or lower. To make it watertight, some potters who work with earthenware glaze their products. However, due to the lower firing temperature, you can still scratch and damage it with a knife. Today, most bricks used in buildings are earthenware, along with terracotta pots for plants and other housewares.
Earthenware is a popular choice for beginner potters. Part of the reason why it’s so popular is because earthenware clay is generally easier for potters to work and is more forgiving. However, it’s also less versatile and more fragile than other types of pottery.
Stoneware
Stoneware appeared after earthenware. It requires higher firing temperatures than earthenware. In most cases, our crew fires our stoneware at temperatures ranging from 2,000° to 2,400° F—hotter than lava from a volcano. Those high temperatures turn the glazes on the outside of the stoneware to glass, or vitrify it.
Unlike porcelain, which is almost always white, potters can make stoneware with multiple different clay colors today. We even combine multiple clay colors into some of our stoneware for a truly unique twist.
Stoneware pottery is strong, hard and nonporous. It’s durable, elegant and versatile; capable of being anything from a customized trophy to a baking dish. In our case, it can also stand up to the heat from a microwave, dishwasher or even an oven under the right conditions. Stoneware also distributes and retains heat more evenly than other types of pottery, so it’s perfect for drinking coffee or tea.
Porcelain
Porcelain was the last type of pottery to reach the west, finally growing in popularity in Europe and North America during the 1700s. On the other hand, it was prized in China even longer for its durability and strength.
Back in the day, potters fired porcelain at even higher temperatures than stoneware. Typically, the final firing temperature ran around 2,600° F.
Today though, the only true difference between how potters make porcelain and stoneware is that porcelain almost always uses white clay. Although it often includes the white mineral kaolin, almost any white clay or even bone ash can do the trick. However, this kaolin is harder for potters to work with and less forgiving than other types of clay. It’s also more fragile in this day and age.
Sculptors can also mold porcelain into more delicate shapes than earthenware or stoneware. Since the 18th century, collectors have prized porcelain because of that, using it to imitate everything from the flowing mane of a horse to the folds of fabric on a dress. With the development of new technology and ideas though, the differences between porcelain and stoneware are becoming fewer and fewer for modern potters.
How is Stoneware Made?
Although stoneware has existed for thousands of years, technology has enabled potters to make it faster and more easily than ever before. There are three main methods for creating stoneware today. These are molding, slipcasting and handcrafting.
Molding
For stoneware, molding is the act of inserting clay into a mold before firing it. Manufacturers use similar processes to produce goods like plastics at scale.
To create mugs, steins and other stoneware products with this process, manufacturers make a mold with hollow portion in the shape of the final product. A liquid slurry of clay and water, called slip, pours into the hole and hardens around the edge of the mold. After the outer edge of the slurry is solid, the liquid interior comes out. Then, the potters remove the mug from the mold. It then dries and goes into the kiln.
Molding is a common way to mass-produce pottery. It’s a cheap, easy method to produce thousands of uniform products. Factories can also use molds to print on designs with a heat press or other printing equipment. However, one of the biggest complaints with molded stoneware is that it’s fragile. Printed designs on these mugs also tend to fade away with time, after years of use and cycles in the dishwasher.
Slipcasting
Slipcasting involves pouring liquid clay into a mold and letting it form a cast inside. Unlike other methods of creating pottery, slipcasting allows for more intricate shapes that potters can’t mass-produce on a pottery wheel. Once the clay is in the mold, it hardens and forms a hollow cast until it can keep its shape. This can take hours to complete, depending on weather conditions. After the piece is dry, makers can glaze it and fire it in the kiln.
While slipcasting allows for shapes that aren’t easily handmade, this type of pottery is fragile. It breaks easily and doesn’t withstand high temperatures, so it’s not always safe to use in the dishwasher, microwave or oven.
Wheel throwing
In spite of the advent of molds and slipcasting, many potters still choose to create stoneware on pottery wheels. Artisans have been doing this for thousands of years. The main mechanism for this method is always the potter’s hands, which better guarantees quality. However, potters can operate their wheels with several different methods, including electric-run or manual wheels, depending on their preferences.
The term “wheel throwing” comes from the start of the process, when the potter literally throws a lump of clay onto the pottery wheel. The potter then centers the clay in the middle of the wheel and forms it, using water and their wet hands to form the clay into the desired shape.
Once the potter shapes the clay, they cut it from the pottery wheel with a thin metal wire. Soon after, the mug, stein or bowl gets a handle or other embellishments to improve its strength.
How to Handcraft Stoneware
The best stoneware pottery mugs are handcrafted on pottery wheels. Even though it takes more time than making stoneware in a mold or slip casting, the manual process lets us make a quality product. Hand thrown pottery mugs are also more durable and has a better hand feel than automatic methods.
Every potter makes mugs a little differently, even within our own facility. However, here is a basic rundown of how we make our stoneware:
1. Throw the Mug
Our stoneware starts as a simple lump of clay that our potters throw onto their pottery wheels. Once they have the lump, or slug, of clay in the center of the pottery, the potter shapes the mug or stein by hand, using a light but firm hand to pull clay upward. Doing this forms the walls of the mug. From there, the potter uses special tools to shape the mug into one of dozens of possible styles.
If you look at the inside walls of your stoneware, you’ll notice ridges all along the inside, plus a swirled pattern of clay at the bottom of the mug. Those are ridges that our potters left behind with their fingertips as they made the mug.
2. Add Handles and Medallions
Once the potters are done making your stoneware mugs or custom beer steins, they come to our handle and medallion crew. Using a delicate hand and an unparalleled eye for detail, they put a handle on your stoneware and place your customized medallion on every piece.
If you look at the base of the handle on one of our mugs, you’ll see a thumbprint. One of our handlers left that thumbprint behind. If you have more than one mug we’ve made, you might also see these thumbprints in different shapes, sizes and styles. Everyone on our team has slightly different thumb shapes and methods of applying handles, so you’ll see the quality of their handcrafted work on full display.
Using top-secret custom technology, our medallion team turns a small piece of clay into your artwork or logo design. They can capture even the most intricate of details, down to realistic leaves on trees or railings on Victorian mansions. Once they’ve captured all the details they possibly can, our medallion team places them on the mug with a hand-applied layer of slip. This slip acts like glue to keep the medallion on the side of the mug.
3. Bisque Firing and Stamping
Stoneware is often fired in a kiln twice in order to make it more durable, but it must air dry so the clay can harden and the water in it can evaporate. If too much water is still in the clay body, the stoneware could break in the kiln. The amount of time it takes for stoneware to dry out enough for its first firing can vary, but luckily our custom HVAC system takes all the variance out of the equation.
Then, our prepping and stamping crew stamps the bottom of your mug using pottery ink, sealing it with wax that withstands the heat of the kilns. Each stamp has our logo sealed to the bottom of your mug, so you can easily tell the mug or stein you’re holding comes from Sunset Hill Stoneware. While you might find some stamps that are unique to our clients, almost all of them will label Sunset Hill Stoneware as the creators of that piece. Every potter has a different way to mark their pottery coffee mugs as their own, including etching their name or impressing it into the bottom of the mug. Stamping is our preferred method.
4. Glazing
When you glaze stoneware, you’re setting it up to have a layer of glass protecting it after the final firing. There are as many glaze colors and combinations as there are pottery studios. Some have glossy or matte finishes, while others are effervescent and have a rainbow-like sheen. Others have dangerous minerals like lead or cadmium in them, so they aren’t safe to use with food or drinks. However, all glazes protect your stoneware and prevent liquid from entering the clay body.
In our case, some of our glazes are solid colors, so our glazing team only has to dip them in the liquid mixture once. But, since we have glazes with two colors or even three, our crew sometimes has to dip the stoneware multiple times to get the desired finish. Some mugs might also need to spend more time in the glaze, depending on how thick or thin the liquid is.
The way some glazes react to the extreme heat of the kilns can be fascinating. While some of our glazes start out life in light orange or brown, some of them can turn an electrifying shade of blue after a night of high-firing. That’s why we’re constantly coming up with new glaze recipes, all of which come from natural minerals. You can check out the tens of dozens of glaze colors and combinations we have available in our Glaze Gallery.
5. Final Firing
Once the glaze is dry, we place the stoneware in the kilns for its final firing. During this final step, the glaze on the outside of the stoneware melts and vitrifies, or turns to glass. It also fuses the glaze to the clay and protects it from the elements.
Despite the high temperatures of the kilns, the final firing is a delicate process. As many potters know, different glazes require different firing cycles depending on the colors they want each piece to be. If something goes wrong in the kiln overnight, a mug we meant to fire in Denim Tuxedo could turn out mustard yellow. Luckily, these misfires are uncommon and we’re always learning more about how each glaze behaves at certain temperatures.
Usually, our crew leaves the kilns to fire overnight. In the morning, they have to open each kiln in stages so the mugs can cool down properly.
What are Ceramic Glazes?
Glazes are any combination of minerals and chemicals that change the color of ceramic pottery. Most potters dip their smallest pieces directly into the glaze. For larger pieces like vases or large bowls though, they might spray or pour the glaze onto it.
Ceramic glazes impart beauty and strength. The glazes used on stoneware almost exclusively come from minerals. During the last firing cycle, the glazes melt and fuse with the mug, so it becomes a thin layer of glass.
There are potentially millions of different recipes for ceramic glazes. Some ceramicists work with glazes that have a rainbow-like luster, while others can be matte or glossy. They can also come from artificial chemicals or from natural minerals. The latter is the case at Sunset Hill Stoneware, where all of our glazes come from mines across the U.S. Some glazes can also contain minerals like lead or cadmium. Sunset Hill Stoneware’s glazes do not.
Like colors in a painting, glazes can impart a different mood or make a statement on each ceramic piece. Solid glazes can run from rustic and understated to vintage or chic. Then there are two- and three-color glazes, which serve to make the piece look even more beautiful while showing a touch of class or patriotism in subtle detail.
Ceramic glazes can change texture and color. In some cases, even the slightest change in the kiln temperature or ratio of minerals can make the colors drastically different. We put our team of mad scientists to the test every once in a while, and the final results we like the most become our newest glaze colors.
Learn more about the subtle differences our glaze colors can have on our blog.
You can see Sunset Hill Stoneware’s growing list of naturally sourced glazes in our Glaze Gallery.
What is the history of stoneware?
Stoneware dates back thousands of years. Some of the earliest pieces of it come from the Indus Valley Civilization in 1900 BCE, in what is now India, Pakistan and Afghanistan. Other early examples come from the Shang dynasty, which ruled China from 1600 BC–1046 BC. They glazed and fired stoneware in kilns and used it to store food, liquids and spices. Even earlier possible examples of stoneware have come from archaeological sites in China dating back to the Paleolithic era, more than 10,000 years ago.
The first examples of stoneware in the United States came from Great Britain and Germany during the colonial era in the late 1600s. The earliest production of stoneware in America began around 1720 in Philadelphia; Yorktown, Virginia; and New York City. These producers used glazes to decorate stoneware, along with designs to mark the contents or manufacturer. Stoneware jars and crocks were essentials until the advent of the modern refrigerator, since they resisted liquid and kept their contents cool all year long. They were also essential for storing preserved food and extending its shelf life through the winter months.
For centuries, potters specializing in stoneware have tried to experiment and improve their craft. Some, such as Doyle Lane, changed the game with glazes you could feel in their pottery. Others, like Adelaide Robineau, changed the way potters painted and glazed their work. George Ohr was another innovative potter who inspires Sunset Hill Stoneware even today.
A self-styled mad potter who lived in Biloxi, Miss., Ohr became famous after his death in 1918 for his highly unusual stoneware pots. His “mud babies,” as he called them, had extremely thin, warped walls and metallic glaze colors. While few potters even today have been able to recreate his ultra-thin walls, his metallic glazes still inspire our work in colors like Root Beer and Silvery Night.
Years after his passing, Ohr’s work was rediscovered gathering dust in the back of a garage in Mississippi. It’s now on display in the Ohr-O’Keefe Museum of Art in his hometown of Biloxi. Art historians also now revere him as the father of abstract-expressionism in America. Even more, he continues to inspire us to leave our mark on the art world in our own way.
The pottery world is full of innovators like Ohr. From Ohr to to our own crew members like Jason Sonsthagen, dozens of potters have left their mark on how they make stoneware for years to come.
Stoneware is an art form that doesn’t typically get as much publicity today as other types of pottery. However, our potters still enjoy working with it to this day. You can still find our master potter, Jason Sonsthagen, at work making larger than life vases and custom stoneware pieces for members of our community in our shop almost every day.
How is stoneware used today?
Stoneware is still a household item even today. Mold-formed stoneware is a popular choice for plates and dinnerware in retail shops. It’s also a classic choice for chafing dishes, crocks and other pieces you can use in cooking.
Because Sunset Hill Stoneware products are safe in the microwave, oven and dishwasher, they’re perfect for cooking everything from omelets in a mug to French onion soup. Because our stoneware retains heat well, it’s also the most elegant choice you can make for having your coffee in the morning.
On the other hand, stoneware is also good at keeping beverages cold. Why do so many breweries choose our stoneware for their annual mug club’s custom beer steins? Because it keeps the beer from warming to room temperature faster than traditional beer glasses and is a statement piece few can forget. While it’s not always a good idea to put your stoneware beer mugs in the freezer, they can still keep your favorite drinks ice cold longer.
Stoneware is also the favorite material for bakers across the world. Because it distributes heat evenly in the oven, stoneware baking stones and jelly roll pans are perfect for baking everything from bread to pizzas in style without bringing a cheap metal sheet into the mix.
Unlike other, more fragile drinkware, our stoneware mugs do not chip easily and can handle years of daily use, making them excellent gifts. Legend in our office even tells of a customer whose company logo mugs survived a fire at their business. This stoneware can potentially last a lifetime, and is guaranteed to add a touch of class to your mug collection.
[…] it’s right in our name, Sunset Hill Stoneware already knows that stoneware makes the best gift. Why though? Aside from the handcrafted quality that comes with an […]
[…] You can learn more about all things stoneware on this page. […]
[…] for you. While some of our team members listen to podcasts or music while they’re making your quality stoneware, several listen to audio books and read at […]
[…] up of stoneware and has a reactive glaze […]
[…] but not as high enough in comparison to porcelain. Stoneware requires temperatures of between 2,000° F and 2,400° F, while porcelain requires a firing temperature of around 2,600° […]
[…] plug outlet of 110V. The Elanze Designs warmer is made up of high quality and thick material of ceramic stoneware. It works best with the candle jar of standard size. You just have to place the candle on the jar […]
[…] using a subpar product for their morning pick-me-up: cheap, machine-made ceramics. Handcrafted stoneware coffee mugs are the superior experience for anyone needing something to hold their drink. Although […]
[…] become your customer’s favorite. Countless reviews from our end users describe how the stoneware they received from a vendor or a relative is now the only mug they’ll use for their coffee. […]
[…] we potentially find shortcuts to making these works of art? Sure. Would the quality of your coffee mugs suffer because of it? Absolutely. That’s just […]